AI-FORM 工业案例
案例 I: DOE 研究模型空间
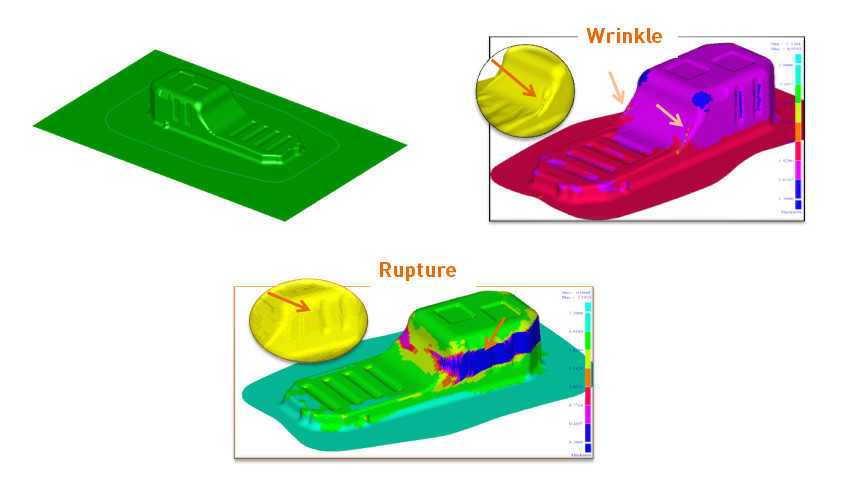
初始模拟的结果,显示成形后的零件存在严重的皱纹和断裂问题
项目背景
- 汽车油箱形状复杂,深度不匀,压边面积小,零件存在巨大深度落差的鞍部,非常容易起皱和断裂。需要通过优化调整压边力,压延筋的分布和初始板材的大小来平衡材料流动,避免缺陷。
- 通常的技术手段是手工调试方案组合,结合冲压加工仿真程序,对方案进行评估。但是耗时时间长,效率低下,而且很难找到最佳解和工作区间。因此,需要采用集成一体全自动化的优化方法。辅助工程师的方案选型,提高设计效率,节省时间成本。
优化策略
根据初始模拟的结果,确认对如下几何和变量进行优化,寻找其最佳工作窗口:
- 冲压板材的尺寸 (下图中BS的偏移量)
- Drawbead的位置和长度(DB1和DB2的值)
- Drawbead压延力的大小,从而确定其形状和尺寸。
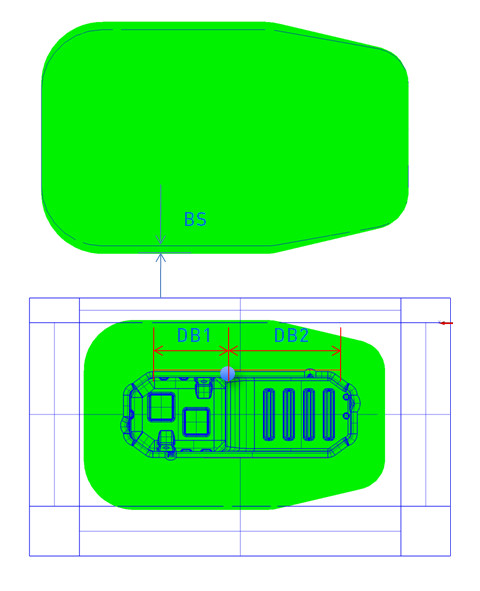
优化策略中的输入参数示意图
优化准则
根据初始模拟的结果,将优化目标定义成以下三个目标变量:
- 在鞍部选择一个区域,根据最大厚度判断是否存在皱纹;
- 在板材上定义传感器,获取最终的板材流入尺寸;
- 在零件顶端定义一个区域,获取FLD的累积值,判断是否发生断裂。
优化步骤
由于工艺范围很宽,对各输入变量与输出结果间的关系尚不清晰且对最佳工作窗口无法预估,也无法预知输入条件中是否存在满足最终产品要求的工艺窗口,因此采取两步进行优化。
第一步: 用DOE寻找可行的工艺窗口
第二步: 采用PSO优化工艺窗口
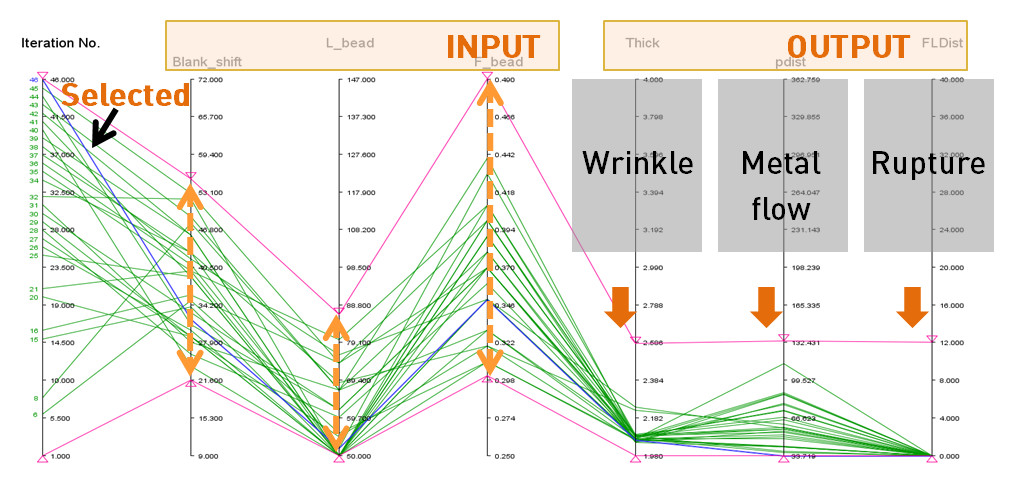
T调整平行坐标取值后PSO分析的结果
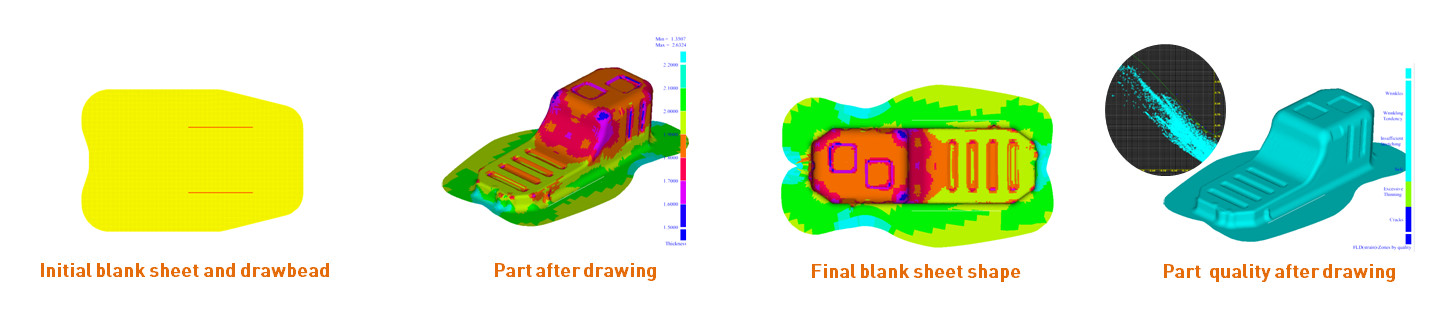
优化工艺区间内的模拟结果(46号)
由于PSO分析是基于DOE分析的结果,所以结果取值范围已有明显的改善。通过调节输出结果轴,可以看到,当板材几何尺寸偏移量介于21~63, 压延筋长度介于50~89,压延阻力系数介于0.29~0.4的范围内,都能获得满意的冲压结果。
项目总结
- C可现实CAD驱动的自动优化
- 可优化任何尺寸和参数,包括几何尺寸、材料参数、过程工艺条件等。
- 完全自动化的有限元网格划分和边界条件定义,无需人工干预。任何模拟参数均可作为优化准则
- 无限的输入变量和输出结果
- 多种优化算法:DOE,GA 和 PSO
- 附带专业的优化结果过滤与分析工具,例如帕累托图,平行坐标图等
- 支持并行计算和并发优化。
案例 II: 物理模型空间
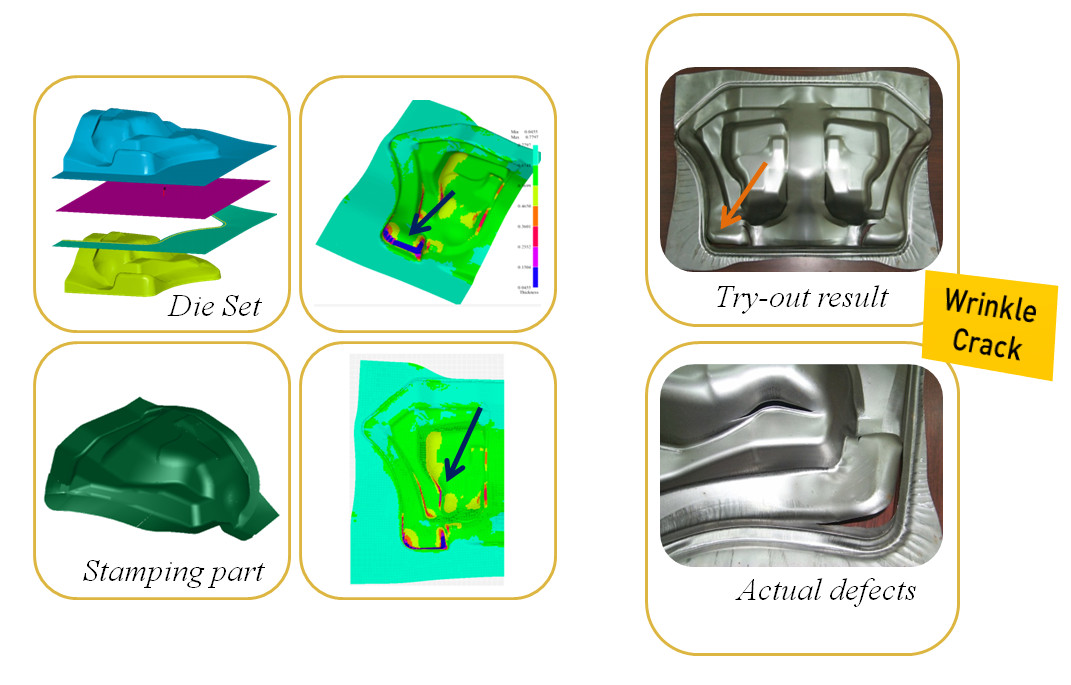
初始设计:模拟结果与实际试模结果比较
项目背景
- 冲压产品的成形性往往受到其本身几何特征的诸多限制,特别是那些远离入口圆角的特征,控制的手段非常有限。这样在实际冲压中解决起来往往效果不佳。
- 通过修改模面,在压料阶段尽量蓄积更多的材料,在皱纹和断裂之间进行巧妙的平衡是非常有效的解决方法。但由于问题的非线性,如果只是通过有限数量的手工修改,在缺乏人工智能指导的情况下是非常困难的。
- 本案例针对某汽车零件,说明采用CAD直接驱动优化解决零件断裂问题的流程和实施要点与解决策略。
优化阶段
1, 优化板材形状和大小
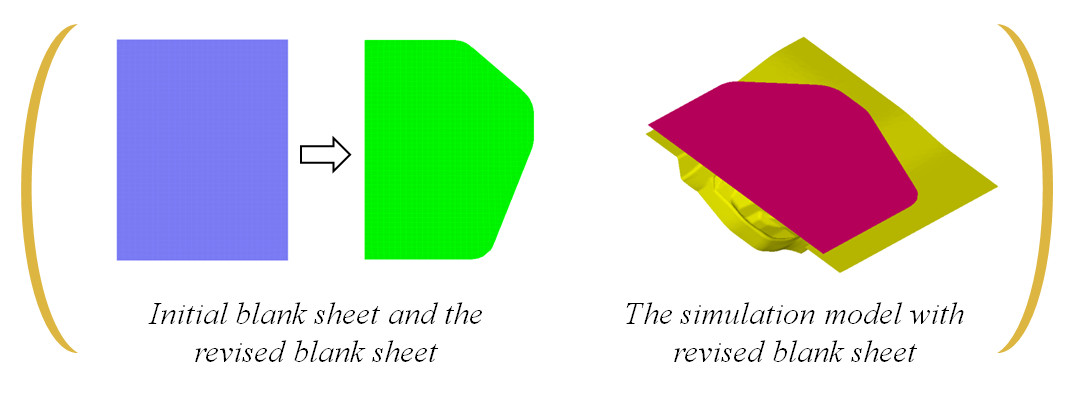
2, DOE了解物理问题
- 了解冲压物理问题的实质, 寻找到解决问题的策略,并提取其中影响入料的特征部分,如本例中的H1和H2,进行参数化研究。
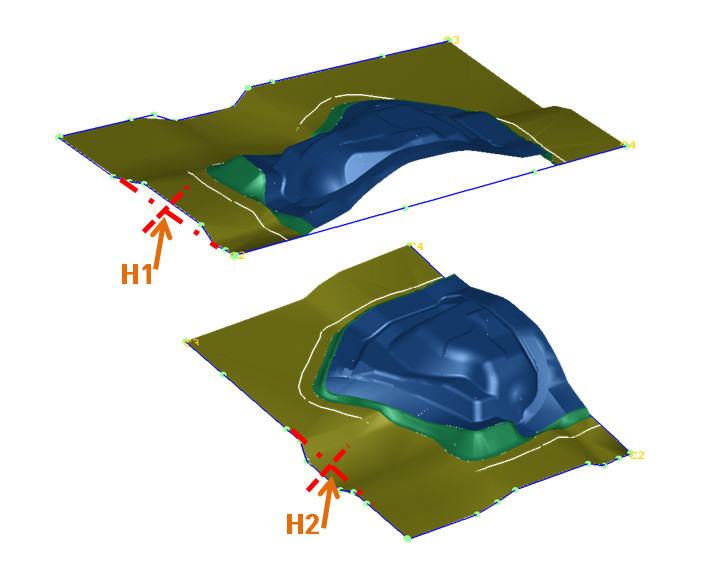
ParaCAD 模型
- 优化工艺参数: 压延力, 摩擦系数
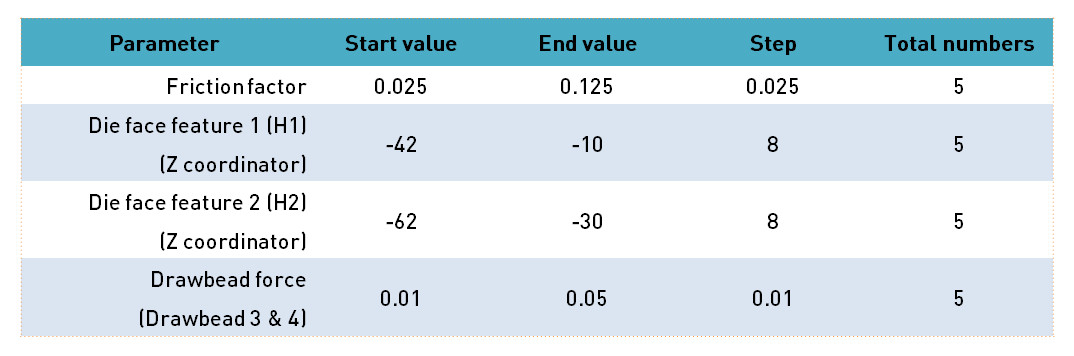
3, 最佳工作窗口
模面参数H2和摩擦系数是主要因数,而模面参数H1和压延筋阻力是次要因数。 图中显示了各变量的影响比例。
从结果分析,以下的工作窗口,均可获得高质量和冲压件。
- 摩擦系数: 0.04 to 0.05
- H2: -55.0 to 30.0
- H1: -42 to -10
- 压延力大小: 0.01 to 0.05
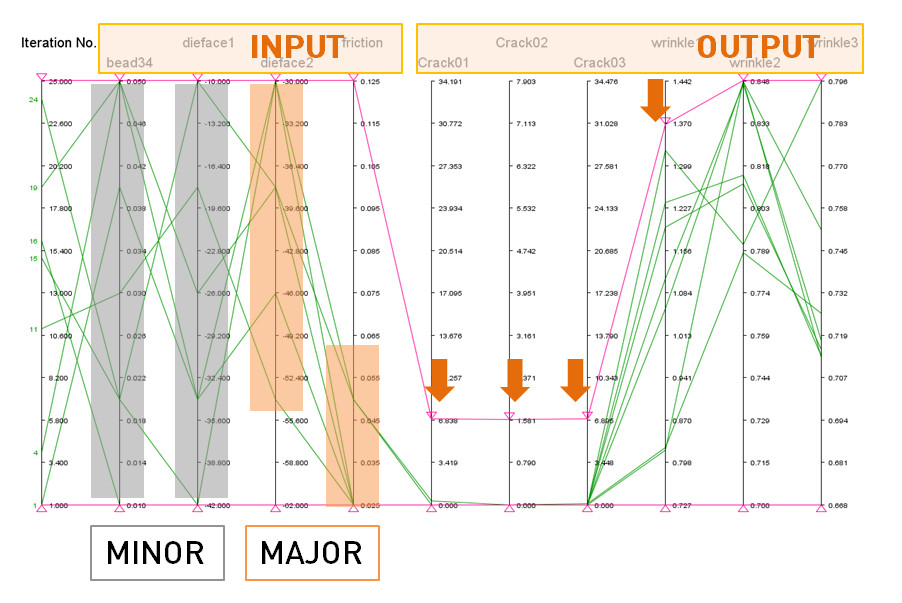
图中显示了各变量的影响比例。
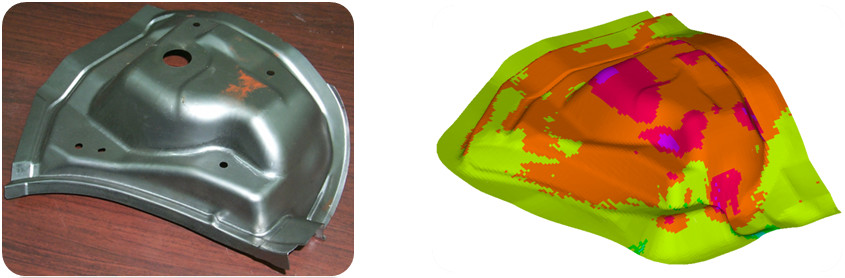
批量生产零件与模拟结果比较
(云图为厚度分布)